Publications Library
Dive into a curated selection of publications and guides that serve as a roadmap through the intricacies of EU Battery Regulation.
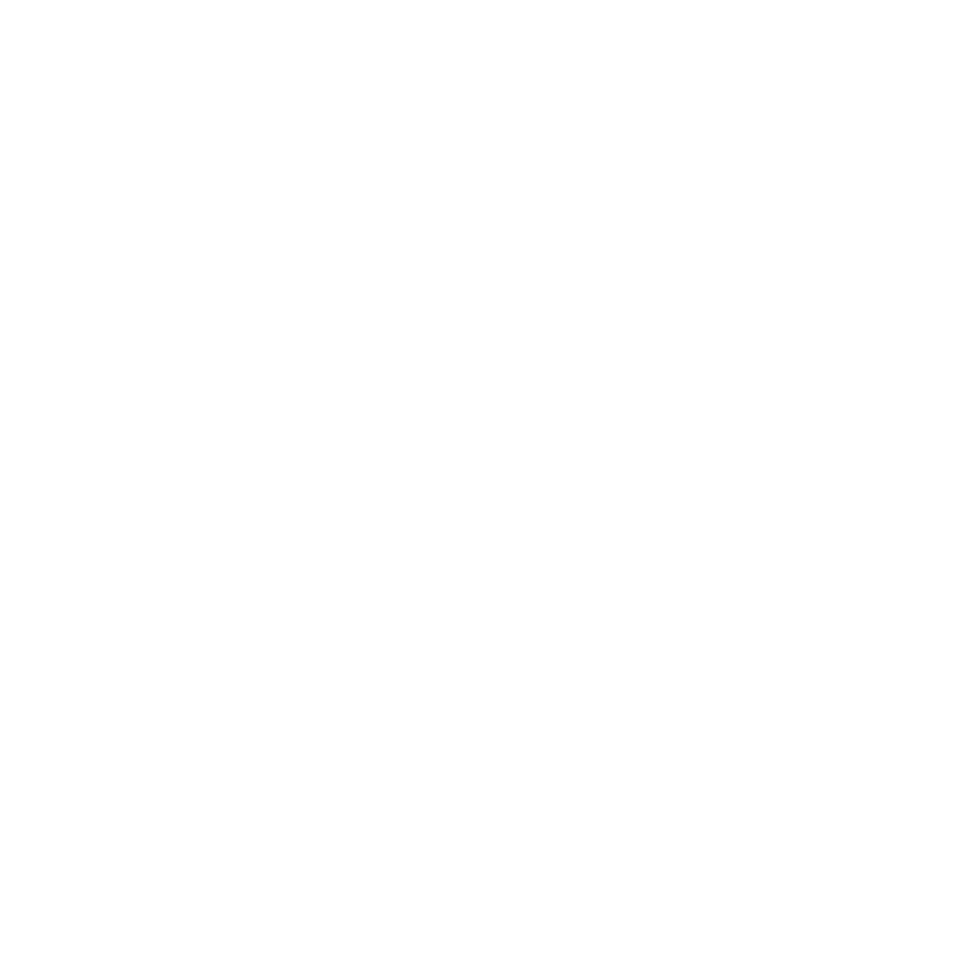
Take a look!
Latest Publications and Guides
Content Type: Whitepaper
Authors: Prof. Dr.-Ing. Achim Kampker, Prof. Dr.-Ing. Heiner Heimes, Dr.-Ing. Christian Offermanns, Robert Ludwigs, Paul Lingohr, Marcel Drescher, Mirčo Krsteski, PhD. Kalle Ylä-Jarkko, Dr.-Ing. Christoph Deutskens, Nico Gossen
Publisher: Production Engineering of E-Mobility Components (PEM) of RWTH Aachen University, Elisa IndustriQ, PEM Motion, camLine
The increasing digitization in today’s production facilities has generated a vast amount of available and usable data ranging from process and machine data to data from inline quality inspections. These present an opportunity for valuable insights and benefits for both production processes and products. To leverage the knowledge from those data, the application of data analytics is a necessity. Read more…
Content Type: Whitepaper
Authors: Prof. Dr. Achim Kampker MBA, Prof. Dr. Heiner Heimes, Sarah Wennemar, Gerrit Bockey, Peter Stellbrink, Bernhard Hukelmann
Publisher: Production Engineering of E-Mobility Components (PEM) of RWTH Aachen University, hs-tumbler GmbH
The mixing process is the first process step in the production of conventional lithium-ion batteries. It is crucial for the quality of the battery and has one of the greatest influences on the subsequent cell performance. In the mixing process, active material, binders and conductive additives are mixed with a solvent to form a so-called slurry. Different equipment is used for this process step, and this equipment can be divided into different types of operation. Read more…
Content Type: Whitepaper
Authors: Prof. Dr.-Ing. Achim Kampker, Prof. Dr.-Ing. Dipl.-Wirt.-Ing. Heiner Hans Heimes, Dr.-Ing. Christian Offermanns, Moritz Frieges, Julian Callard, Nima Ghandily, Jonas Gorsch, Maximilian Graaf, Adrian Herrmann, Niklas Kisseler, Benedikt Späth, Simon Quinker
Publisher: Production Engineering of E-Mobility Components (PEM) of RWTH Aachen University
Battery safety is a multifaceted approach that should be considered on all levels of cell and battery pack design. The main hazard when operating a lithium-ion cell is thermal runaway, which occurs when the cell generates more heat than it can dissipate. When a threshold temperature is reached, the runaway becomes unstoppable and the stored energy will be released in the form of heat and burnable gases. The main triggers for a thermal runaway are either electrical, mechanical, thermal, contamination, or manufacturing defects. Read more…
Content Type: Whitepaper
Authors: Prof. Dr.-Ing. Achim Kampker, Prof. Dr.-Ing. Heiner Heimes, M. Sc. Benjamin Dorn, M. Sc. Daniel Neb, M. Sc. Sebastian Wolf, Dr.-Ing. Alexander Arndt, Dr.-Ing. Simon Britten, Dipl.-Ing. Richard Hendel
Publisher: Production Engineering of E-Mobility Components (PEM) of RWTH Aachen University, LASERLINE GmbH
“The drying of electrodes for LIBs is the most expensive process step in the entire battery production, accounting for over 20% of the total production costs. The process innovation of laser drying offers great potential to revolutionize electrode manufacturing. The main advantages of the diode laser drying technology are high energy efficiency due to direct energy input as well as footprint reduction and possible quality improvements. Depending on the selected hybrid drying configuration, this results in up to 30% lower OpEx on a gigafactory scale, which can realize cost savings of several million euros per year and per line. Read more…
Content Type: Whitepaper
Authors: Dr. Heiner Heimes, Henning Clever, Artur Scheibe, Dr. Phillipp Hypko, Johannes Metten, Philipp Kölbe
Publisher: Production Engineering of E-Mobility Components (PEM) of RWTH Aachen University, FlexFactory
Pioneering the field of consumer electronics, lithium-ion batteries (LIB) are present in an everincreasing number of applications. With properties such as high energy density, fast charging capability, and extended cycle life, they are outperforming competing electrochemical energy storage systems and have established themselves as the leading battery technology. Current development forecasts show that battery demand and production volumes will witness unprecedented growth rates in the coming years. Europe in particular is rapidly catching up in terms of battery cell production capacities and expects future production volumes to increase tenfold to around 1.5 TWh in 2030. Read more…
Content Type: Electric Mobility Guide
Authors: Dr.-Ing. Dipl.-Wirt.-Ing. Heiner Hans Heimes, Prof. Dr.-Ing. Achim Kampker, Ansgar vom Hemdt, Kim D. Kreisköther, Dr. Sarah Michaelis, Ehsan Rahimzei
Publisher: Production Engineering of E-Mobility Components (PEM) of RWTH Aachen University, VDMA
The following guide focus on the manufacturing processes of the active materials and the electrolyte. Subsequently, the electrode foil, the separator and the cell housing production are described. Read more…
Content Type: Electric Mobility Guide
Authors: Dr.-Ing. Dipl.-Wirt.-Ing. Heiner Hans Heimes, Prof. Dr.-Ing. Achim Kampker, Ansgar vom Hemdt, Kim D. Kreisköther, Dr. Sarah Michaelis, Ehsan Rahimzei
Publisher: Production Engineering of E-Mobility Components (PEM) of RWTH Aachen University, VDMA
The manufacture of the lithium-ion battery cell comprises the three main process steps of electrode manufacturing, cell assembly and cell finishing. The electrode manufacturing and cell finishing process steps are largely independent of the cell type, while cell assembly distinguishes between pouch and cylindrical cells as well as prismatic cells. Read more…
Content Type: Electric Mobility Guide
Authors: Dr.-Ing. Dipl.-Wirt.-Ing. Heiner Hans Heimes, M. Sc. Benjamin Dorn, M. Sc. Daniel Neb, M. Sc. Henning Clever, M. Sc. Artur Scheibe, Dr. Sarah Michaelis, Jörg Schütrumpf
Publisher: Production Engineering of E-Mobility Components (PEM) of RWTH Aachen University, VDMA
With their ability to efficiently store large amounts of energy temporarily and then make them available as needed, battery systems in the form of battery modules and battery packs play a key role in the energy supply of the future. This is not only due to the increasing demand for electric vehicles and stationary energy storage systems, but also to the recognized need to drive the energy transition and reduce dependence on fossil fuels. Read more…
Content Type: Press Release
Publisher: Production Engineering of E-Mobility Components (PEM) of RWTH Aachen University
The Chair of Production Engineering of E-Mobility Components (PEM) of RWTH Aachen University has joined forces with Volkswagen’s battery subsidiary PowerCo and Jagenberg Converting Solutions in the “MiKoBatt” research project funded by the German Federal Ministry of Education and Research. The partners are looking into ecological, economical, and sustainable production of battery cells in order to give German and European manufacturers a commercial competitive edge in the future. Specifically, factory and machine concepts are to be developed for this purpose that allow efficient battery cell production with the help of so-called microenvironments. Read more…
Content Type: Research Paper
Authors: Achim Kampker, Heiner Hans Heimes, Benjamin Dorn, Henning Clever ,Robert Ludwigs ,Ruiyan Li, Marcel Drescher
Publisher: MDPI, Production Engineering of E-Mobility Components (PEM) of RWTH Aachen University
This paper presents an approach for the design and derivation for establishing a digital product twin for battery cells. A digital product twin is a virtual replica of a physical battery cell and can be used to predict and optimize quality properties and performance in real-time. The study focuses on pouch cell manufacturing and aims to map the large amount and variety of process information down to purchased parts and interim products. The approach for this study was to collect and analyze data from the physical production process and use this information to structure a digital battery product twin based on its product architecture. The main findings of this study indicate that a digital product twin can be effectively structured and implemented in a digital interface based on its product architecture in combination with data from the physical production process. The results of this study show the potential of digital product twins, in which statements about material, design, and behavior can be made using real information from production. Further research will focus on the practical application and implementation of digital product twins in a battery cell pilot production. Read more…
Content Type: Research Paper
Authors: Achim Kampker, Heiner Hans Heimes, Benjamin Dorn, Henning Clever, Robert Ludwigs, Ruiyan Li, Marcel Drescher
Publisher: MDPI, Production Engineering of E-Mobility Components (PEM) of RWTH Aachen University
The drying of electrodes for lithium-ion batteries is one of the most energy- and cost-intensive process steps in battery production. Laser-based drying processes have emerged as promising candidates for electrode manufacturing due to their direct energy input, spatial homogeneity within the laser spot, and rapid controllability. However, it is unclear to what extent electrode and cell quality are affected by higher heating and drying rates. Hybrid systems as a combination of laser- and convection-based drying were investigated in an experimental study with water-processed LFP cathodes. The manufactured electrodes were compared with purely laser-dried and purely convection-dried samples in terms of drying times and quality characteristics. The electrodes were characterized with regard to physical properties like adhesion and electronic conductivity, as well as electrochemical performance using the rate capability. Regarding adhesion and electronic conductivity, the LFP-based cathodes dried in the hybrid-drying process by laser and convection showed similar quality characteristics compared to conventionally dried cathodes, while, at the same time, significantly reducing the overall drying time. In terms of electrochemical performance, measured by the rate capability, no significant differences were found between the drying technologies used. These findings demonstrate the great potential of laser- and convection-based hybrid drying of LFP cathodes to enhance the electrode-drying process in terms of energy efficiency and operational costs. Read more…
Content Type: Research Paper
Authors: Heiner Heimes; Christian Offermanns; Moritz Frieges; Nima Ghandily; Ghazi Zamit; Jonas Gorsch
Publisher: IEEE Xplore, Production Engineering of E-Mobility Components (PEM) of RWTH Aachen University
The industry trend for lithium-ion battery cells for automotive applications is moving toward increased cell dimensions. For cylindrical lithium-ion battery cells, the introduction of the 46xx format is an example of this trend. To ensure a long lifetime and safe operation, lithium-ion batteries must be operated within an optimum temperature window. This is managed by cooling the cell with battery module or battery system level cooling strategies. In comparison to the state-of-the-art 21700 cell format, these 4680 lithium-ion battery cells represent an approximately 5.5x volume increase while introducing new cell design challenges: Larger cells can increase the distances between heat generation and the cooling system and require new design approaches for the internal tab configuration. Furthermore, the surface to volume and heat generation ratio shrinks with increasing cell size, leading to challenges for the cooling strategy. This paper analyzes the influence of the cell size and the number of tabs on sidewall and bottom cooling performance of cylindrical lithium-ion battery cells. Therefore, the cooling effectivity of sidewall and bottom wall active cooling of 18650, 21700, 4680 cell formats as well as different numbers of tabs was investigated from a thermal perspective. The results indicate a change of optimal cooling strategy depending on cell dimensions and number of tabs, showcasing performance optimization potentials for module and cell design. Read more…
Content Type: Contribution to a conference proceedings
Authors: Jan Felix Plumeyer, Nils Menebröker, Henning Clever, Lukas Kokoyinski, Saskia Wessel, Heiner Hans Heimes, Achim Kampker
Publisher: Universitätsbibliothek RWTH Aachen University, Production Engineering of E-Mobility Components (PEM) of RWTH Aachen University, Fraunhofer Research Institution for Battery Cell Production
The European Union’s ambitious climate targets will make climate-friendly storage technologies essential. More than any other, this decade could be marked by battery technology, especially the lithium-ion battery (LIB). In addition, various trends in mobility and consumer electronics are spurring the cross-industry use of this secondary storage device. As a result, the need for additional production capacities is rising, and the need for vertical integration of the value chain of LIB in Europe. In current forecasts, Europe has a considerable deficit between battery cell demand and production capacities. The deficit highlights the need for additional capacities and effort to develop new production systems. Furthermore, production technologies remain challenging, as high reject rates are expected initially, and a reduction of costs at the battery cell level is mandatory. Formation and aging as part of the cell finishing are the production steps with the highest processing time and space requirements. The formation can take up to 24 hours, and the subsequent aging between 8 to 36 days. It thus represents the biggest bottleneck. Read more…
Content Type: Contribution to a conference proceedings
Authors: Jan Felix Plumeyer, Nils Menebröker, Henning Clever, Lukas Kokoyinski, Saskia Wessel, Heiner Hans Heimes, Achim Kampker
Publisher: Universitätsbibliothek RWTH Aachen University, Production Engineering of E-Mobility Components (PEM) of RWTH Aachen University, Fraunhofer Research Institution for Battery Cell Production
The cell finishing process is the final stage in the production of a battery cell. Almost one third of the production costs of a battery cell are related to this part of the production. It includes a series of steps and technologies aimed at optimizing the battery cell’s performance, quality, and safety. The process is divided into three categories: pre-treatment, formation procedure, and quality testing. The order of the processes and the time required for each step can vary depending on the manufacturer and the cell format. Recent trends in optimizing the cell finishing process include the integration of a second filling process for larger prismatic cells and the optimization of the formation protocol or Electrochemical Impedance Spectroscopy (EIS) as possible methods for quality inspection. Efforts are also being made to reduce the pre-treatment time and improve the degassing process to ensure cell performance, quality, and safety. In this paper, all process steps of the cell finishing process are presented, and their function and technological implementation in the industry are explained. Future innovations are analyzed in terms of time to market and the potential to optimize the process in terms of quality, time, and cost. Read more…
Content Type: Research Paper
Authors: Achim Kampker, Heiner Hans Heimes, Christian Offermanns, Janis Vienenkötter, Tobias Robben
Publisher: MDPI, Production Engineering of E-Mobility Components (PEM) of RWTH Aachen University
In this paper, battery system architectures are methodologically derived in order to find the key type differences. In a first step, the system levels are identified and distinguished. In order to be able to completely cover the solution space of battery system architectures, a distinction is also made between mono- and multifunctional materials. Based on the system levels, a framework for possible architectures is derived. Four system architecture generations with a total of eight different types are identified and analyzed in the dimensions “Nomenclature”, “Approach”, “Omitted Components” and “Industry Examples”. In this way, upcoming system architectures, such as cell-to-pack and cell-to-chassis, can be clearly differentiated. Finally, fundamental product characteristics for the four system generations are derived and compared. Read more…
Content Type: PhD Dissertation
Authors: Christian Offermanns, Achim Kampker (Thesis Advisor), Robert H. Schmitt (Thesis Advisor)
Publisher: Apprimus Verlag, Production Engineering of E-Mobility Components (PEM) of RWTH Aachen University
Due to the rapidly growing demand for automotive battery cells, it is necessary to optimize battery cell production economically and in terms of production output. The consideration of defined characteristic values shows that the sub-step of finalization or process step formation represents a bottleneck. In order to increase the output of the production line as well as to reduce the product costs per gigawatt hour by a guarantee of a constant or improved quality of the existing and future production lines, it is necessary to understand the cause-effect relationships of the processes. Based on the objective and investigation of problem-relevant scientific literature, clear deficits can be identified in the investigation of environmental conditions (mechanical stress and ambient temperature) during the formation of lithium-ion battery cells. Read more…
Content Type: Battery Atlas
Authors: Gerrit Bockey, Heiner Heimes
Publisher: Battery-News.com
“Battery-News.de” presents an up-to-date overview of planned and already implemented projects in the field of lithium-ion battery production. As usual, the corresponding data are taken from official announcements of the respective players and battery production sources. Learn more…
Content Type: Battery Atlas
Authors: Gerrit Bockey, Heiner Heimes
Publisher: Battery-News.com
“Battery-News.de” presents a current overview of planned and already implemented projects in the field of module and pack production of lithium-ion batteries. The corresponding data comes as usual from official announcements of the respective stakeholders and from sources on battery production. Learn more…
Content Type: Battery Atlas
Authors: Gerrit Bockey, Heiner Heimes
Publisher: Battery-News.com
“Battery-News.de” presents a current overview of companies in the field of lithium-ion battery production. The corresponding data comes as usual from official announcements of the respective stakeholders. Featured are companies that can cover at least one process step from dosing/mixing to end-of-line testing of battery packs. Learn more…
Content Type: Battery Atlas
Authors: Natalia Soldan, Gerrit Bockey, Heiner Heimes
Publisher: Battery-News.com
“Battery-News.de” presents a current overview of planned and already implemented projects in the field of lithium-ion battery recycling. The corresponding data comes from official announcements of the respective stakeholders and reliable sources on battery production. Learn more…
Content Type: Battery Atlas
Authors: Gerrit Bockey, Heiner Heimes
Publisher: Battery-News.com
“Battery-News.de” presents a current overview of companies in the field of quality assurance for lithium-ion batteries. The corresponding data comes as usual from official announcements of the respective stakeholders and from sources on battery production. Learn more…
Content Type: Battery Atlas
Authors: Niklas Kisseler, Gerrit Bockey, Heiner Heimes
Publisher: Battery-News.com
“Battery-News.de” presents a current excerpt of European test centers for batteries and battery systems. The corresponding data comes as usual from official announcements of the respective stakeholders and from sources on battery production. Learn more…
Content Type: Battery Atlas
Authors: Gerrit Bockey, Heiner Heimes
Publisher: Battery-News.com
“Battery-News” presents a current overview of European cell producers focusing on the next generation of battery technologies (Next-Gen). The companies are at various stages of development, from prototypes to large-scale manufacturing. The data is based on official announcements from the stakeholders and reliable sources within the battery production industry. Learn more…
Content Type: Whitepaper
Authors: Heiner Heimes, Achim Kampker, Benjamin Dorn, Christian Offermanns, Gerrit Bockey, Sarah Wennemar, Henning Clever, Konstantin Sasse, Janis Vienenkötter, Nikolaus Lackner, Wolfgang Bernhart, Jan-Philipp Hasenberg, Tim Hoty, Dennis Gallus, Kostantin Knoche, Iskender Demir, Theresa Haisch
Publisher: Production Engineering of E-Mobility Components (PEM) of RWTH Aachen University, Roland Berger
The first gigafactories are starting up, while further cell production facilities are still being built – this is the status of European cell production in 2022. The battery as the main component of the decarbonization of transport and accelerator of the energy transition is currently experiencing further global growth. Production capacities of six to nine terawatt-hours are expected to be reached by the end of the decade. In the competition to meet the projected demand, countries and companies are dueling along the entire value chain. Read more…
Content Type: Book
Authors: Achim Kampker, Heiner Hans Heimes
Publisher: Springer Vieweg
This book is an “Open Access” publication on the state of development of electromobility. There is no doubt: the automotive industry is undergoing a profound transformation. With electromobility, traditional vehicle and propulsion concepts are fundamentally changing. Defined by new vehicle components such as the battery, power electronics, electric motor, and fuel cell, the entire value chain is changing. This work provides a comprehensive overview of the challenges and solutions in all areas: from product development to the production of electric vehicles, to the establishment of infrastructure, novel business models, and the potential of sustainability. Read more…
Content Type: Press Release
Publisher: Production Engineering of E-Mobility Components (PEM) of RWTH Aachen University
The Chair of Production Engineering of E-Mobility Components (PEM) of RWTH Aachen University has published a carbon footprint calculation tool for commercial vehicles on the internet. The online traffic target calculator is able to take into account various fleet stocks for the year of 2030 as well as different infrastructure scenarios and compare their effect on current emission targets and their costs. According to the RWTH institution, heavy commercial vehicles in particular cause an above-average proportion of CO2 emissions in German road traffic across all vehicles. Nevertheless, the focus of the current political debate is mainly on the large number of passenger cars. Read more…
Content Type: Battery Atlas
Publisher: Battery-News.com
“Battery-News.de” presents a current overview of planned trade fairs and events for lithium-ion batteries. The corresponding data comes as usual from official announcements of the respective stakeholders and from sources on battery production. Learn more…
Content Type: Press Release
Publisher: Production Engineering of E-Mobility Components (PEM) of RWTH Aachen University
The Chair of Production Engineering of E-Mobility Components (PEM) of RWTH Aachen University has joined forces with numerous partners from science and industry to launch the DemoRec project funded by the German Federal Ministry of Education and Research. The aim of the three-year project is to develop practical solutions for the automated dismantling of electric vehicle batteries. Read more…
Content Type: Battery Atlas
Authors: Merlin Frank, Heiner Heimes
Publisher: Battery-News.com
“Battery-News.de” presents a current excerpt of European companies directly involved in or supporting second-life applications of batteries. The map is divided into five categories: Collection and transport to the facility, identification and condition assessment, end-of-life strategy selection, technical refurbishment and integration and installation. Read more…
Content Type: Training
Author: Systemiq, PEM Motion
Publisher: ITAS
The automotive sector is undergoing a transformation, and the circular economy is becoming a crucial factor for its long-term success. This tailored courses provide you with a unique opportunity to understand and shape this transformation from two crucial perspectives:
Course 1: Circular Cars – Made in Saxony: Strategic Implementation for Business Leadership
In this course, entrepreneurs and business leaders gain valuable insights into the strategic implementation of circular economy principles into their corporate strategy. Learn how transitioning to a circular approach not only promotes environmental sustainability but also enhances competitiveness. From waste reduction to the development of innovative business models, this course guides you towards the sustainable transformation of your organization.
Course 2: Circular Cars – Sustainable Practices in the Workplace: Implementation for Skilled Workers
This course is designed for skilled workers in the automotive industry, offering practical insights into the application of circular economy principles in the workplace. Learn how to use resources more efficiently, minimize waste, and improve the quality of your work. By engaging in these practices, you not only contribute to environmental protection but also enhance your professional qualifications and contribute to your company’s competitiveness. Learn more…
Content Type: Report
Authors: Dr. Susanne Kadner, Dr. Jörn Kobus, Prof. Dr. Martin R. Stuchtey, Prof. Dr.-Ing. Thomas Weber
Publisher: Circular Economy Initiative Deutschland
We are living through times of great change: innovative technologies are being developed at breakneck speed, patterns of consumer behaviour are changing fast, value chains which have hitherto been separate are linking up to create new solutions, capital markets are driving an enthusiasm for new business models and, last but not least, the state is providing more direction and investment. Read more…
Content Type: Electric Mobility Guide
Authors: Dr.-Ing. Dipl.-Wirt.-Ing. Heiner Hans Heimes, Prof. Dr.-Ing. Achim Kampker M.B.A., M. Sc. Christian Offermanns, M. Sc. Kim D. Kreisköther, Prof. Dr.-Ing. Arno Kwade, M. Sc. Stefan Doose, M. Sc. Marco Ahuis, M. Sc. Peter Michalowski, Dr. Sarah Michaelis, Ehsan Rahimzei, Dr. Sarah Brückner, Karl Rottnick
Publisher: Production Engineering of E-Mobility Components (PEM) of RWTH Aachen University, Battery LabFactory Braunschweig, VDMA, VDMA Waste and Recycling Technology Association
The amount of lithium-ion batteries (LIBs) in their “end of life” (EoL) will increase significantly in the coming years due to the growing market penetration of electric vehicles, which is why new concepts for recycling and raw material recovery must be developed. The process scrap generated in battery production will ensure a need for higher recycling capacities in the near future. To implement sustainable EoL concepts, all players along the value chain from material synthesis to battery cell, battery module, and battery pack production to the use phase must address this issue. Read more…
Content Type: Press Release
Publisher: Production Engineering of E-Mobility Components (PEM) of RWTH Aachen University
The Chair of Production Engineering of E-Mobility Components (PEM) of RWTH Aachen University launches a consortium study titled “Mastering the Challenges of a Batteryʼs Second Life”. Together with numerous industrial partners, the focus is on the question of whether and how aged traction batteries from electric vehicles can be profitably reused as stationary energy storage systems. Learn more…
Content Type: Press Release
Publisher: Production Engineering of E-Mobility Components (PEM) of RWTH Aachen University
Shortly before the updated EU Battery Regulation comes into force, the chair “Production Engineering of E-Mobility Components” (PEM) of RWTH Aachen University has published a study on the European battery recycling market. Due to high investment costs, the current structure of the value chain will move toward large recycling centers, according to the analysis published jointly with “PwC Strategy&”. According to the analysis, after initial overcapacities, the recycling market will be fully utilized from 2030 onwards, requiring investments of more than 2.2 billion euros for the annual processing of around 570,000 tons of battery material. Read more…
Content Type: Research Paper
Authors: Achim Kampker, Heiner Hans Heimes, Christian Offermanns, Merlin Frank, Domenic Klohs and Khanh Nguyen
Publisher: MDPI, Production Engineering of E-Mobility Components (PEM) of RWTH Aachen University
Life cycle strategies for traction batteries, such as remanufacturing, reuse, and recycling of retired automotive lithium-ion batteries (LIBs), have received growing attention, as large volumes of LIBs will retire in the near future and the demand for LIBs continues to grow. At the same time, the relevance of the sustainability of a battery system over its entire life cycle is increasing as factors such as the EU Battery Regulation provide greater market and product transparency. As a result, research and industry require forecasts in order to assess the future market situation and to make well-founded decisions. Therefore, this paper provides forecasts of the return volumes of battery systems from BEVs and PHEVs up to 2035. Additionally, a representative European battery pack for PHEVs and BEVs was evaluated for each year since 2013, based on the ten vehicles with the largest market share in each year until 2021. In addition, the battery return streams are divided into three different 3R strategies based on expert interviews in order to evaluate the upcoming workload in these areas. The term “3R” refers to the sum of the currently existing pathways around reuse, remanufacturing, and recycling. In 2030, about 38.8 GWh will return and enter the recycling process annually. For battery reuse, about 13 GWh will return every year from 2030 onwards, ready to be used in stationary storage for energy transition. Compared to this, battery remanufacturing is expected to be supplied with a slightly lower volume of approximately 11 GWh per year. Read more…
Content Type: Research Paper
Authors: Achim Kampker, Heiner H. Heimes, Christian Offermanns, Moritz H. Frieges, Maximilian Graaf, Natalia Soldan Cattani, Benedikt Späth
Publisher: MDPI, Production Engineering of E-Mobility Components (PEM) of RWTH Aachen University
Mass transport conversion to an electrified powertrain requires suitable strategies for processing electric vehicle (EV) batteries after their intended first service life. Due to aging mechanisms, EV batteries lose capacity over their period of use and become unsuitable for their initial application at some point. However, to expand their lifetime and to meet the sustainability demand for EVs, the usage of these batteries in so-called Re-X applications is under intense discussion. Until now, downstream processing has been subject to high uncertainty regarding the expected advances. While many issues on the technical and ecological side have been at least partially resolved, the economics are still under assessment. For this reason, this paper intends to give a well-based outlook on the costs and benefits of three chosen scenarios: reuse, repurpose, and recycle. It is expected that under the given national policies and global market conditions, growing quantities of retired EV batteries will return from the transportation markets. Consequently, the market potential for retired batteries in downstream applications will significantly increase, as well as calls for stable solutions. Read more…
Content Type: Research Paper
Authors: Achim Kampker, Heiner Hans Heimes, Christian Offermanns, Janis Vienenkötter, Merlin Frank, Daniel Holz
Publisher: MDPI, Production Engineering of E-Mobility Components (PEM) of RWTH Aachen University
Lithium-ion batteries (LIBs) have been proven to be increasingly popular and are the solution of choice for many companies and business models around the world. One major question for battery owners is how to deal with returning batteries if they still contain sufficient capacity for operation. In this case, those energy storages can still be used in different, less-required second-life applications, such as stationary battery storage systems, contributing to increased product sustainability and economic benefits at the same time. However, the second-life business model is still at an early stage of development due to the young EV market in combination with long vehicle lifetimes. As a consequence, there are several barriers in various thematic fields, complicating the rededication process for LIBs. This review paper focuses on a summary of barriers to second-life adoption published with scientific reference. Furthermore, barriers are clustered thematically to provide a transparent landscape picture and valuable insights into the rededication process of LIBs. Read more…
Content Type: Battery Atlas
Authors: Benedikt Spath, Jonas Gorsch, Heiner Heimes
Publisher: Battery-News.com
“Battery-News.de” presents an up-to-date overview of planned and already implemented projects in the field of cell-level components of lithium-ion batteries. As usual, the corresponding data are taken from official announcements of the respective players and from battery production sources. Learn more…
Content Type: Battery Atlas
Authors: Gerrit Bockey, Heiner Heimes
Publisher: Battery-News.com
“Battery-News” presents a current excerpt of the cell chemistries and formats currently used by battery manufacturers in Europe. The corresponding data comes from official announcements of the respective stakeholders and from sources on battery production. Learn more…
Content Type: Battery Atlas
Authors: Gerrit Bockey, Heiner Heimes
Publisher: Battery-News.com
“Battery-News.de” presents a current overview of planned and already implemented projects in the field of active materials for lithium-ion batteries. The corresponding data comes as usual from official announcements of the respective stakeholders and from sources on battery production. Learn more…